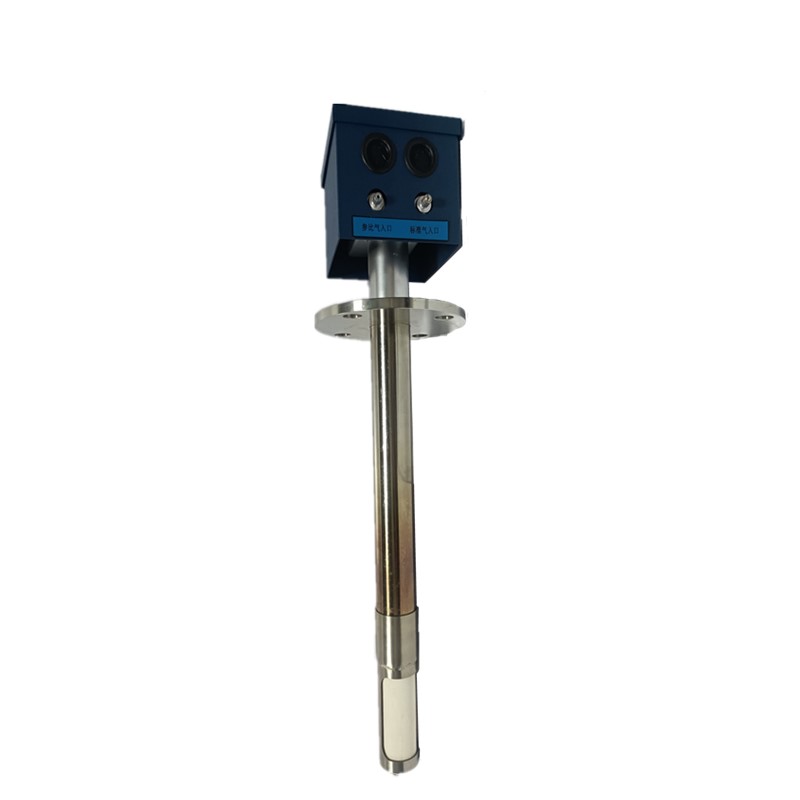
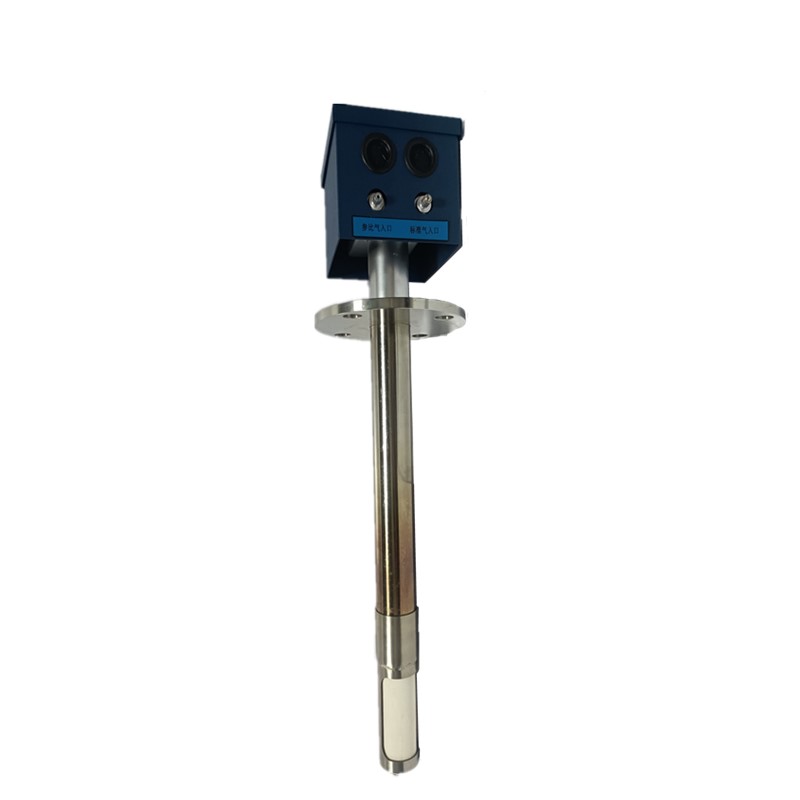
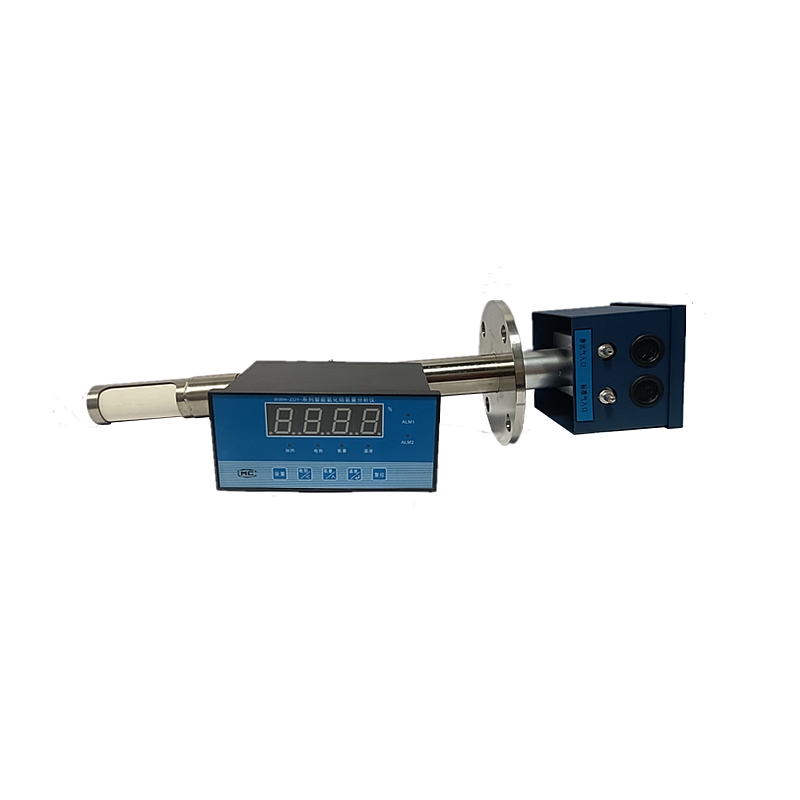
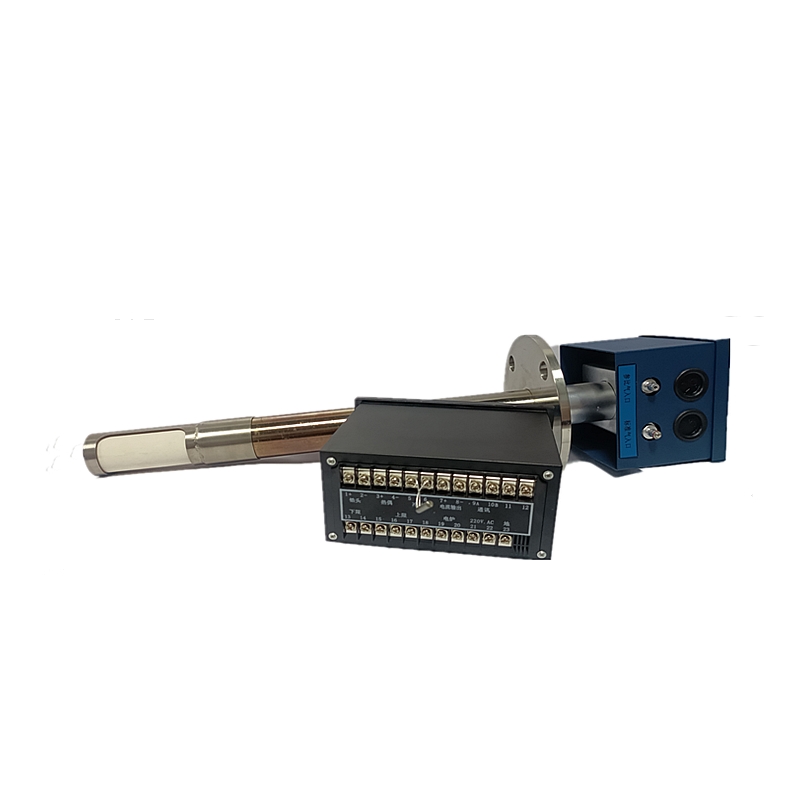
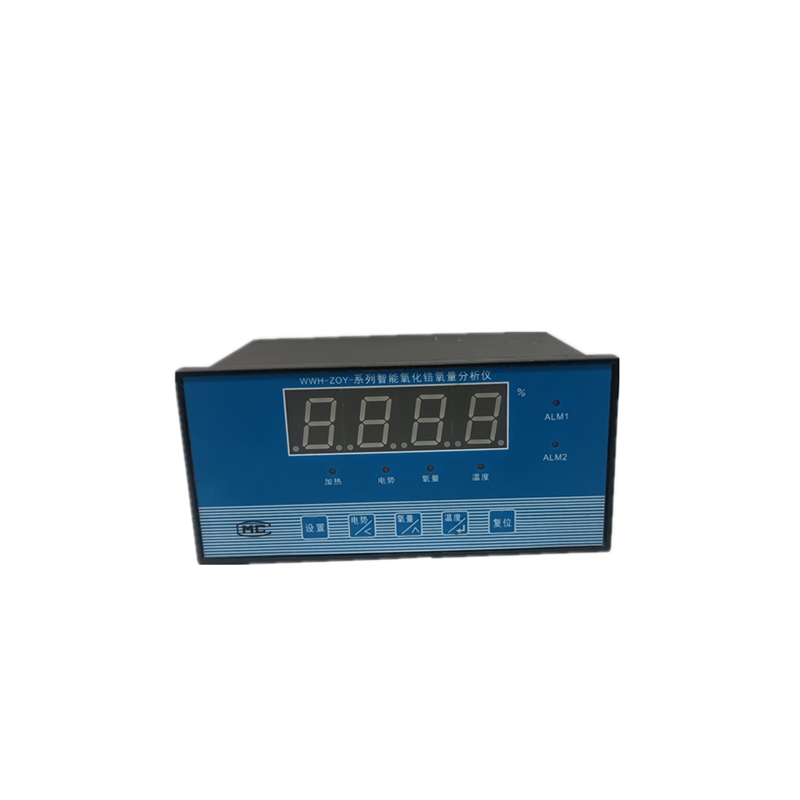
Zirconia Oxygen Analyzer
Zirconia o2 Analyzer
High accuracy and wide range ratio
Features
• Measured flue gas temperature:
ZOY-4 type is lower than 700 °C (low temperature type)
ZOY-5 type 700 ~ 1200 °C (high temperature type)
• Output signal:
May expand the two-circuit isolation output,0~10mA DC and 4~20mA DC,
adopts the electro-optical isolation. Direct networking with computer
• Zirconia probe heating furnace heating time: about 20 minutes
• Environmental Condition:0~50℃;Relative Humidity<90%
• Power Source:220V±10%,50Hz
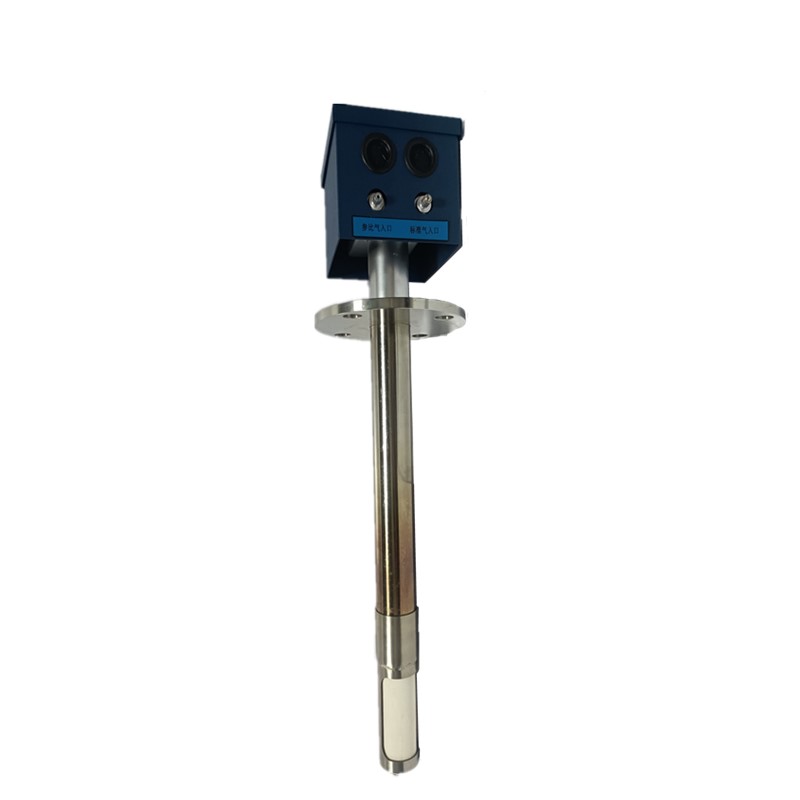
Description
Reviews
Zirconia Oxygen Analyzer Overview
Intelligent zirconia oxygen analyzer is a practical and reliable automatic analysis instrument. Zirconia o2 analyzer can cooperate with various electric unit instruments, conventional display and recording instruments and DCS distributed control system, and can quickly and accurately detect and analyze the flue gas content generated during the combustion process of boilers, kilns, heating furnaces and other combustion equipment. In order to realize low-oxygen combustion control, achieve the purpose of energy saving and reduce environmental pollution. Zirconia oxygen analyzer is widely used in the measurement of oxygen content in high temperature working conditions such as electric power, metallurgy, petrochemical, environmental protection, heating, ceramics, glass and metal heat treatment. The zirconia oxygen analyzer is called zirconia o2 analyzer, also called zirconia oxygen analyser.
WWH-ZOY-2000 series intelligent zirconia oxygen analyser consists of ZOY type zirconia probe (primary instrument) and ZOY oxygen transmitter (secondary instrument).
Zirconia Oxygen Analyzer Working Principle
Zirconia material is a zirconia solid electrolyte, which is a stable zirconia ceramic sintered body formed by doping a certain amount of calcium oxide or yttrium oxide in pure zirconia and sintering at high temperature. Since zirconia o2 analyzercontains oxygen ion holes in its cubic lattice, zirconia forms a solid electrolyte at high temperature and has the property of conducting oxygen ions. The measured gas (flue gas) passes through the probe filter and enters the inner side of the zirconia tube, and the reference gas (air) enters the outside of the probe zirconia tube through natural convection. When the oxygen concentration inside and outside the zirconia tube is different, an electromotive force of oxygen concentration difference will be generated between the inside and outside of the zirconia tube.
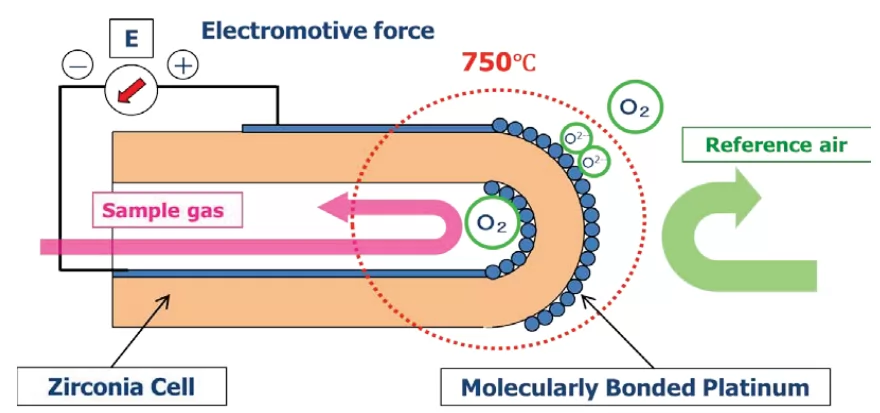
Zirconia Oxygen Analyzer Technical Parameter
Zirconia Oxygen Analyzer Technical Parameter | |
Basic error | <±2%F•S, meter accuracy level 1 |
Range | 0 ~ 5% O2; 0 ~ 10% O2; 0 ~ 20% O2; 0 ~ 25% O2 |
Background correction | -20mV ~ +20mV |
Measured flue gas temperature | ZOY-4 type is lower than 700 °C (low temperature type) ZOY-4 type 700 ~ 1200 °C (high temperature type) |
Output signal | Scalable dual isolated output, 0~10mA DC and 4~20mA DC, optically isolated, directly connected to the computer. |
Load capacity | 0 ~ 1.2 Κ Ω or 0 ~ 600 Ω |
Environmental conditions | 0 ~ 50 ° C; relative humidity <90% |
Power supply | 220V±10%, 50Hz |
Power consumption | The transmitter is about 8W, and the heating furnace is about 50W on average. |
Response time | 90% for about 3 seconds |
Zirconia probe life | zirconia tube is guaranteed for one year according to international GB11169-89. The life of the main body is more than 5 years. |
Heating time | Zirconia probe heating furnace heating time: about 20 minutes |
Zirconia Oxygen Analyzer Zirconia probe installation
★ Selection of installation point:
The flue gas temperature at the installation point of the probe shall meet the requirements of less than 600 C. Generally speaking, the flue gas temperature is low, and the probe has a long service life, high flue gas temperature, and a short service life. The probe shall not be installed at the dead angle where the flue gas does not flow, nor in the place where the flue gas flows quickly (such as the expansion cavity of some bypass airway).
In addition, it is required that the flue gas leakage is small and the probe installation and maintenance is convenient. For medium and small boilers, it is recommended to install it behind the superheater in front of the economizer, because the flue gas of the boiler system flows from the furnace to the drum, passes through the superheater, economizer and air preheater, and is discharged from the chimney by the induced draft fan after recovery. If the measuring point is too close to the outlet of flue gas furnace. due to the high temperature and fast flow rate, the stainless steel shell of the probe will be scoured and corroded, reducing the service life; if the measuring point is too biased, due to the air leakage in the flue gas system, the oxygen value at the measuring point will be high, which can not accurately reflect the oxygen content of flue gas in the furnace.
★ Probe fixing flange on furnace wall:
The transition frame is made of steel as shown in Figure 6. The flange of the transition frame can be directly welded on the outer wall of the furnace wall or embedded in the furnace wall, but it is required to be airtight and firm. The flange at the other end of the transition frame is designed to fix the detector, so it must match the screw hole of the fixed flange of the detector. If the 12mm mounting hole is used, four 12mm mounting holes shall be evenly distributed on the D 130mm circle of the transition flange. and four M10 X 40 screws shall be used to fasten it with the fixed flange of the detector. In order to prevent air leakage, rubber cardboard sealing ring can be filled between the two flanges.
★ Probe installation:
The reference gas of the probe is provided by the natural convection of air, The probe needs to be installed horizontally, and the interface between the reference gas and the standard gas should face down correspondingly. The rubber paperboard must be filled between the mounting flange of the probe and the flange of the transition frame to avoid air leakage into the flue and affect the measurement accuracy.
The probe end must be more than 150 mm away from the inner wall of the boiler to make the exposed part of the porous ceramic of the filter back to the flow direction of the flue gas (the direction of the filter can be rotated separately) so as to avoid the ceramic body being scoured by the gas and extend the service life.
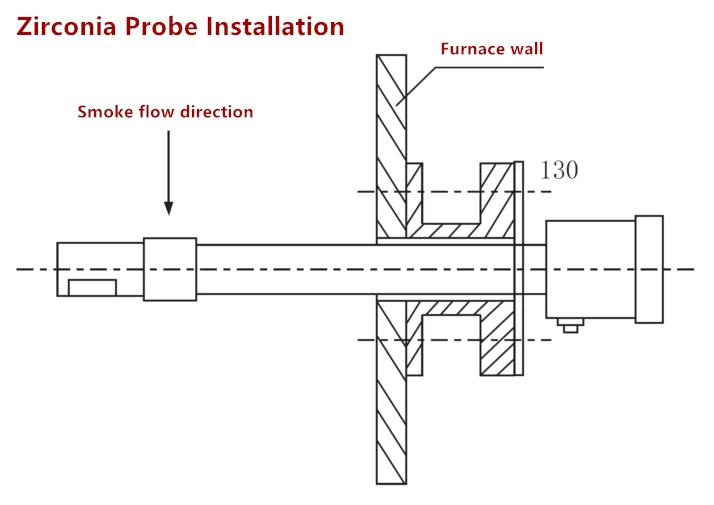
Note: If you want to insert the oxygen probe into a medium with a higher temperature, when inserting, please insert the probe slowly in sections, each time inserting 1/3 of the length of the probe, after each section, wait for 3 minutes to 5 minutes, wait for the probe rod to warm up Then insert them all. In order to avoid the rapid change of temperature from breaking the ceramic and glass parts inside the oxygen probe.
How to Choose the Zirconia Oxygen Analyzer?
·The flue temperature and pressure
·The flue composition and density
·Insertion depth of probe or probe adapter
·Washing and explosion protection of the measured medium
·Adapter installation type,function, and explosion class
·Installation conditions applicable on site
Company Profile
CN BOILER ENGINEERING SOLUTION LLC is a comprehensive service provider of thermal energy systems in China, devoted to providing customers with one-step thermal energy system solutions by safe, save energy, environmentally, intelligent, and reliable. Main products include industrial boilers(hot water boilers, steam boilers, thermal oil boilers, waste heat boilers, and CFB boilers), steam generators(electric steam generators, electric hot water generators), intelligent control system by PLC control, PLC+PC control or DCS control, remote instrument and valves, and so on. The control system includes industrial boiler control system(oil fired boilers, gas fired boilers, biomass fired boilers, coal fired boilers, electric boilers, waster heat boilers, CFB boilers), PLC deaerator control system, condensate recovery system, reactor control system, heating exchanger control system, hot air boiler control system, etc. The remote instrument and valves include temperature sensors, pressure transmitters, pressure sensors, pressure controllers, liquid level meters, flowmeters, electric control valves, Zirconia, TDS sewage, and so on.
Share your thoughts
Showing
6
of
0
reviews
Most recent
Top Reviews
Read more
Your rating
Your review *
Name *
Enter your Name
Email *
Enter your Email
Upload Image
Notice: Ensure your image is no larger than 200KB before uploading.
Submit
Contact Us Now
Enter your inquiry details, We will reply you in 24 hours.
Name can't be empty
E-mail can't be empty
Company can't be empty
Phone can't be empty
Phone
Products can't be empty
Products you want
Message can't be empty
Verification code error
Clear
People who viewed this item also viewed