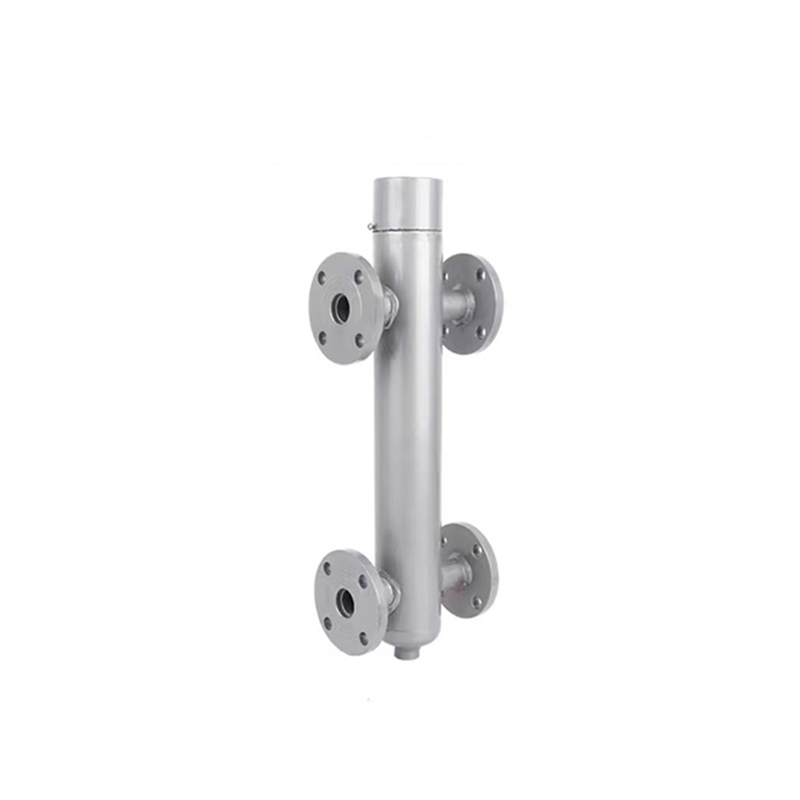
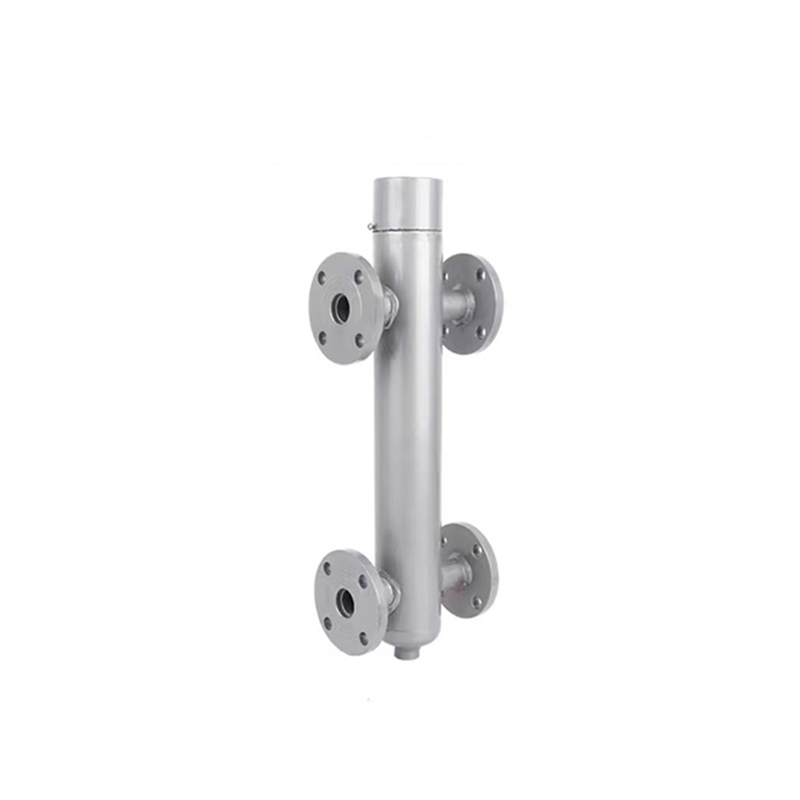
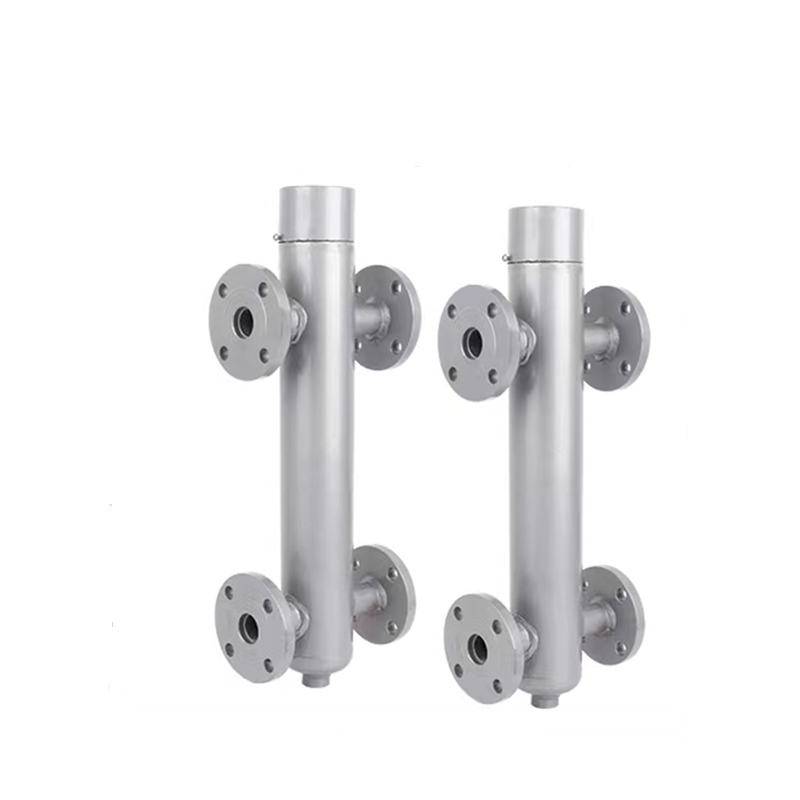
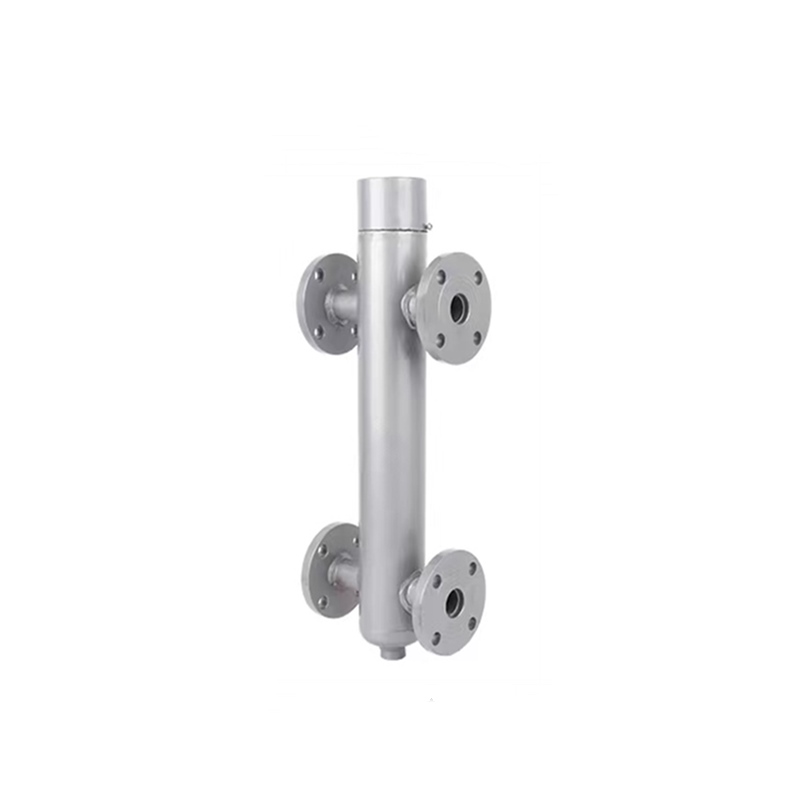
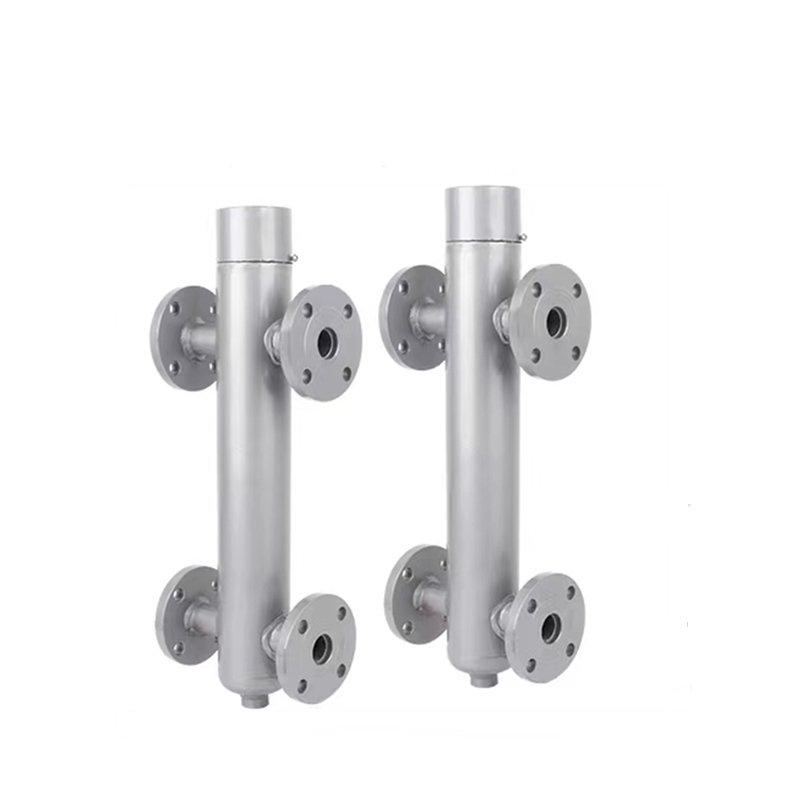
High Low Water Level Sensor
Industrial Water Level Sensor
Easy installation, accurate measurement
Features
• Simple structure/long service life/Color-coded cable cores for easy installation
• flange caliber: DN20, DN25
• Output signal: DPDT signal and 4-20mA
• Medium temperature: ≤250℃
<span style="\"box-sizing:" border-box;\"="">• Type: industrial water level sensor
Promise
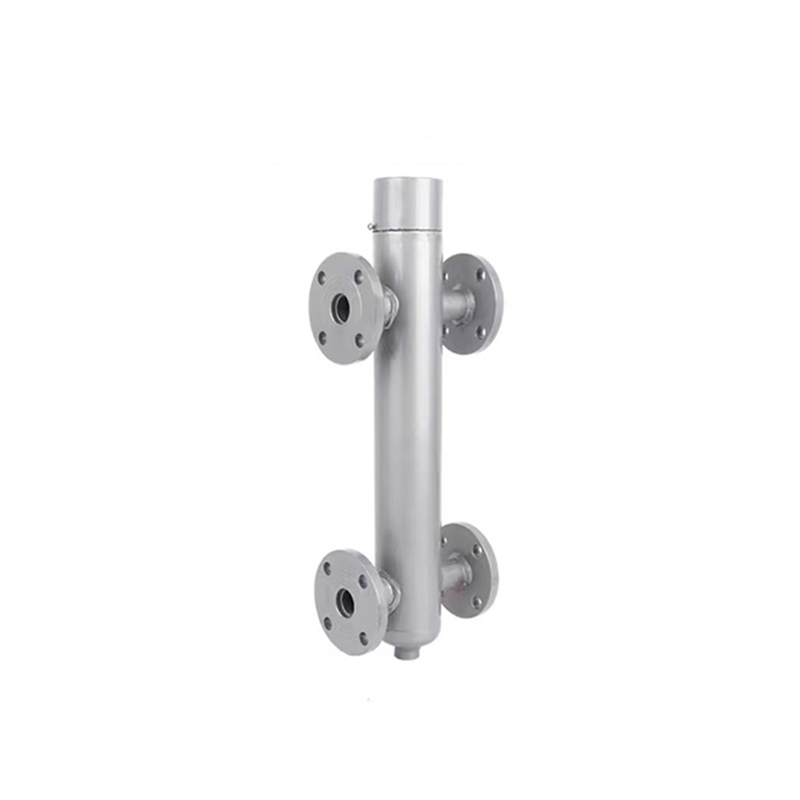
Description
Reviews
High Low Water Level Sensor Overview
The high low water level sensor consists of a cylinder closed by end plates at both ends. It is one kind of industrial water level sensor. It can alarm to indicate stop or start the water pump when the water is high or low, There are five electrode rods of different lengths in the cylinder, and their lengths correspond to different water levels; one end of the electrode rod is fixed on the end plate through a screw plug. On the top, an insulating sleeve is lined between the electrode rod and the screw plug. The electrode rods are of different lengths. Using the conductivity of the water in the boiler, when the water level in the boiler changes, due to the contact and separation of the electrode rods of different lengths and the boiler water of different water levels, the electrical circuit is closed or disconnected, and then the electrical circuit is transmitted outward a signal, which reflects the changes in water level can then be used for further processing. In the above-mentioned electrode type water level sensor, the matching surfaces among the electrode rod, the insulating sleeve, the screw plug, and the end plate all adopt a tapered structure. The electrode type water level sensor uses the conductivity of water as the working principle, the sensing quality is stable, the high low water level sensor is not easy to generate false signals, the structure is simple, and the service life is long.
The high low water level sensor is suitable for petroleum, chemical industry, metallurgy, food, brewing, medicine, chemical fiber, chemical fertilizer and environmental protection, electric power, water supply, and other departments to measure the liquid level of the pressure vessels (such as steam boilers, hot water boiler, steam generator, etc.) or the liquid in the open container, the high low water level sensor can directly display the liquid level on site, and can also be attached to the remote transmission of the liquid level, which can be directly connected to the DCS control system to realize long-distance liquid level monitoring.
High Low Water Level Sensor Structure
The electrode water level sensor comprises a measuring cylinder, an electrode, an electrode connecting cable, and an electrode controller.
· The measuring cylinder facilitates the condensation of saturated steam and vapor while keeping the temperature loss to a minimum.
· The electrodes are made of special stainless steel, the insulator is made of high-purity ceramics, and the pressure seal between the ceramics and the metal body is guaranteed by a vacuum welding process.
· Electrode connection cable cores are color coded for ease of installation and all cables use ring crimp terminals on one end.
· Electrode controller has a dual power supply, outputs DPDT signal and 4-20mA analog signal, and has a system self-test fault alarm function.
High Low Water Level Sensor Features
★ Based on the conductivity of water, the sensing quality is stable and it is not easy to generate false signals
★ Simple structure, long service life
★ Color-coded cable cores for easy installation
★ With system self-test fault alarm function
High Low Water Level Sensor Specification
High Low Water Level Sensor Technical Parameter | |||
Product name | High Low Water Level Sensor | ||
Working temperature | ≤250℃ | ||
Nominal pressure | 2.5MPa(25Bar) | ||
Test pressure | 3.8MPa(38Bar) | ||
Medium range | Water, oil, steam and so on | ||
Output signal | DPDT signal and 4-20mA signal | ||
Installation method | Side installation | ||
Flange caliber | DN20, DN25 | ||
Center distance L | 300/350/440mm | ||
Liquid level control parameter | |||
Center distance L(mm) | Normal level range(mm) | High level alarm(mm) | Low level alarm(mm) |
300 | ±30 | 70 | -60 |
350 | ±35 | 70 | -70 |
440 | ±40 | 80 | -70 |
Remark:the zero position is in the L/2 |
High Low Water Level Sensor Installation
Method
★ Directly connected to the water level gauge, generally embedded between the water level gauge and the flange of the boiler body
★ The inclined water level gauge can be changed into a straight type by using long and short bends, which will not affect the water addition, but also facilitate the observation of the water level.
Precautions during installation
· The electrode number is stamped on the end cap with steel stamps. Electrode No. 1 is extremely high full water level, No. 2 is the high water level, No. 3 is the low water level, No.4 is extremely low water shortage dangerous water level, and No. 5 is the normal water level offline.
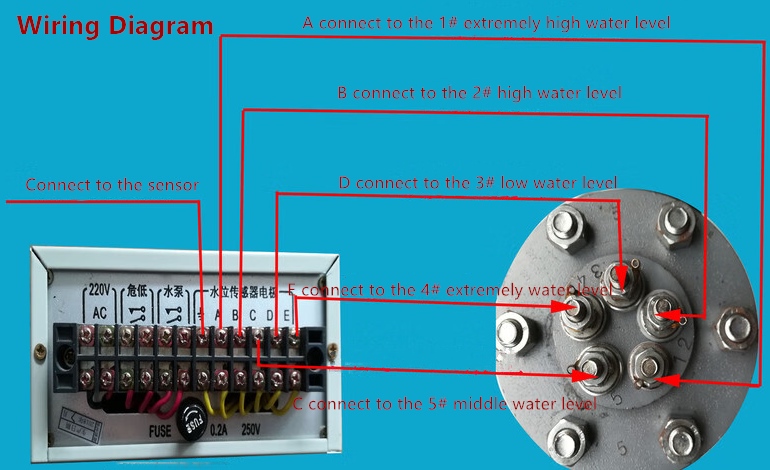
· Lead wires from the electrodes should use high-temperature insulated wires, or put on high-temperature sleeves (porcelain tubes, glass fibers, etc.), to avoid high-temperature melting of the wire sleeves, resulting in short-circuit and failure.
· The flange connecting the boiler and the water column, and the flange connecting the water column and the water level gauge need to cooperate with each other during installation, and try to keep the water column device and the boiler horizontal and vertical.
High Low Water Level Sensor Precautions for Maintenance
★ After installing the boiler self-control water level alarm, attention must also be paid to observing the glass water level. Just in case the safety device fails! When the water level in the boiler is lower than the normal water level, the water should be manually filled in time, and the cause of the failure should be checked immediately. When the water level disappears in the glass tube, methods such as flushing the water level gauge and calling water (that is, hanging water) should be used. When the water column connected to the pipe flange is lower than the false water level caused by the boiler flange, the water column must be lowered and the stored water released before lifting the water, or lifting the water twice in a row. If it is found that the boiler is short of water, it is strictly forbidden to feed water to the boiler to prevent accidents.
★ It is necessary to do a good job of maintenance work on a regular basis, usually once every 3 to 6 months. During maintenance, loosen the six nuts on the end cap and take out the electrode rod, use sandpaper to wipe off the scale on the rod, and put it back as it is.
Troubleshooting Methods
★ When the electric control box does not display or alarm according to the set water level, you can open the cover and check the circuit to see if there is any short circuit, loose joints, and missing grounding wires. Generally, it can return to normal after troubleshooting.
★ If there is no problem with the wiring, use a megohmmeter to check the insulation performance of the line 1, 2, 3, 4, the electrode wiring and the No. 5 flange line connected to the shell should be non-conductive. The resistance should be more than 20 megohms (the water in the water column should be discharged for inspection). If there is no short circuit, It means that the insulating sleeve is faulty, the furnace must be shut down and the pressure reduced to 0°C, the end cover flange should be opened, and the corresponding insulating sleeve should be replaced.
Company Profile
CN BOILER ENGINEERING SOLUTION LLC is a comprehensive service provider of thermal energy systems in China, devoted to providing customers with one-step thermal energy system solutions by safe, save energy, environmentally, intelligent, and reliable. Main products include industrial boilers(hot water boilers, steam boilers, thermal oil boilers, waste heat boilers, and CFB boilers), steam generators(electric steam generators, electric hot water generators), intelligent control system by PLC control, PLC+PC control or DCS control, remote instrument and valves, and so on. The control system includes industrial boiler control system(oil fired boilers, gas fired boilers, biomass fired boilers, coal fired boilers, electric boilers, waster heat boilers, CFB boilers), PLC deaerator control system, condensate recovery system, reactor control system, heating exchanger control system, hot air boiler control system, etc. The remote instrument and valves include temperature sensors, pressure transmitters, pressure sensors, pressure controllers, liquid level meters, flowmeters, electric control valves, Zirconia, TDS sewage, and so on.
Share your thoughts
Showing
6
of
0
reviews
Most recent
Top Reviews
Read more
Your rating
Your review *
Name *
Enter your Name
Email *
Enter your Email
Upload Image
Notice: Ensure your image is no larger than 200KB before uploading.
Submit
Contact Us Now
Enter your inquiry details, We will reply you in 24 hours.
Name can't be empty
E-mail can't be empty
Company can't be empty
Phone can't be empty
Phone
Products can't be empty
Products you want
Message can't be empty
Verification code error
Clear
People who viewed this item also viewed