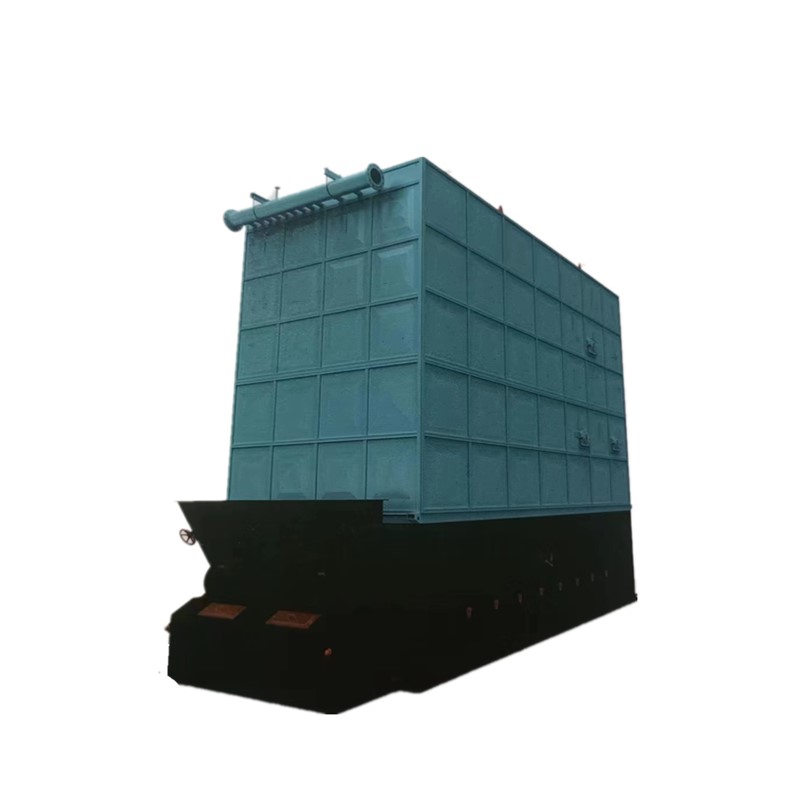
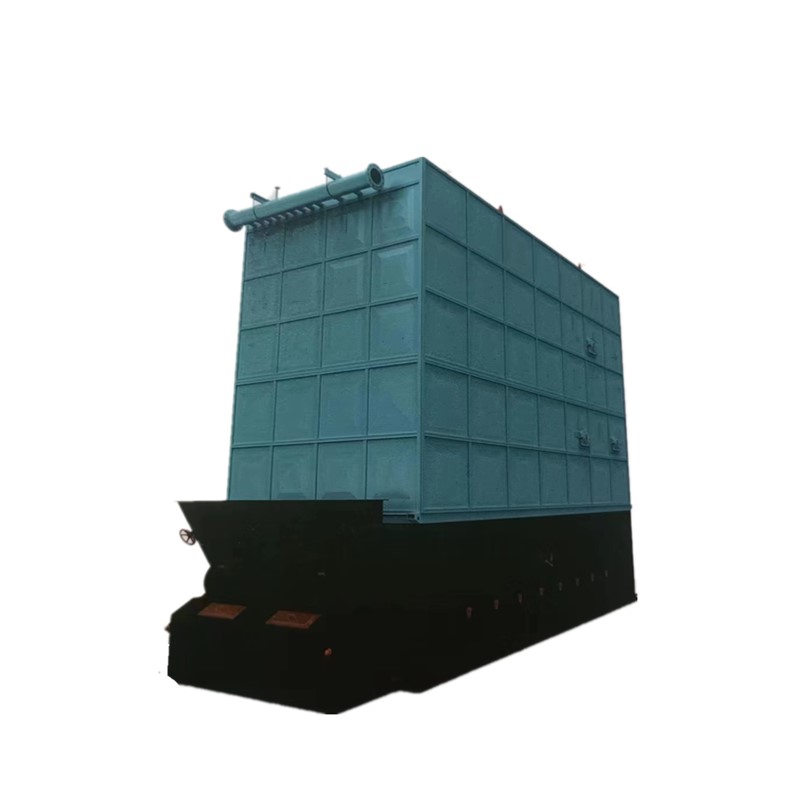
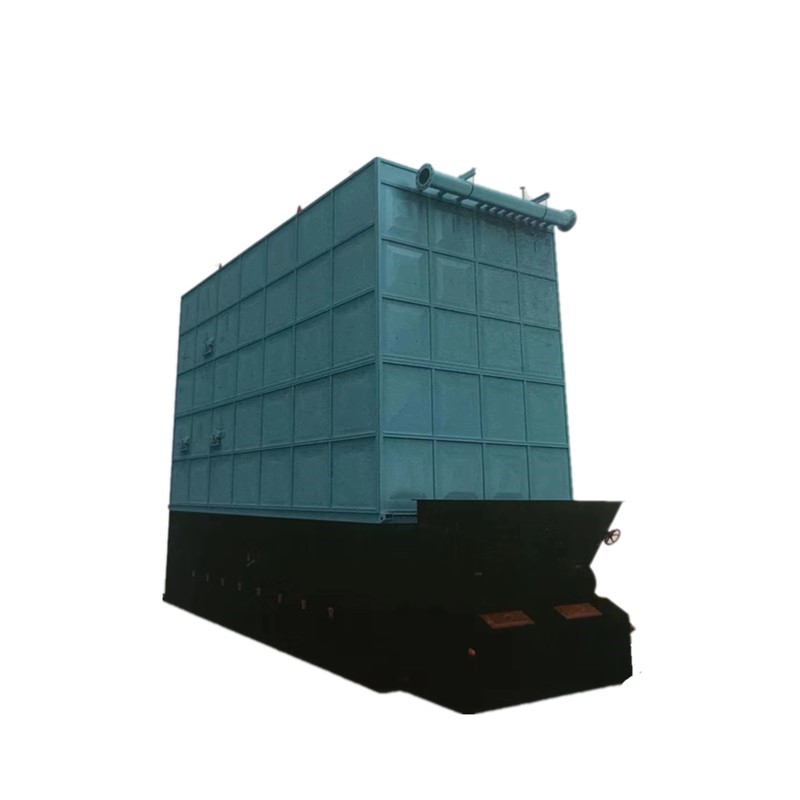
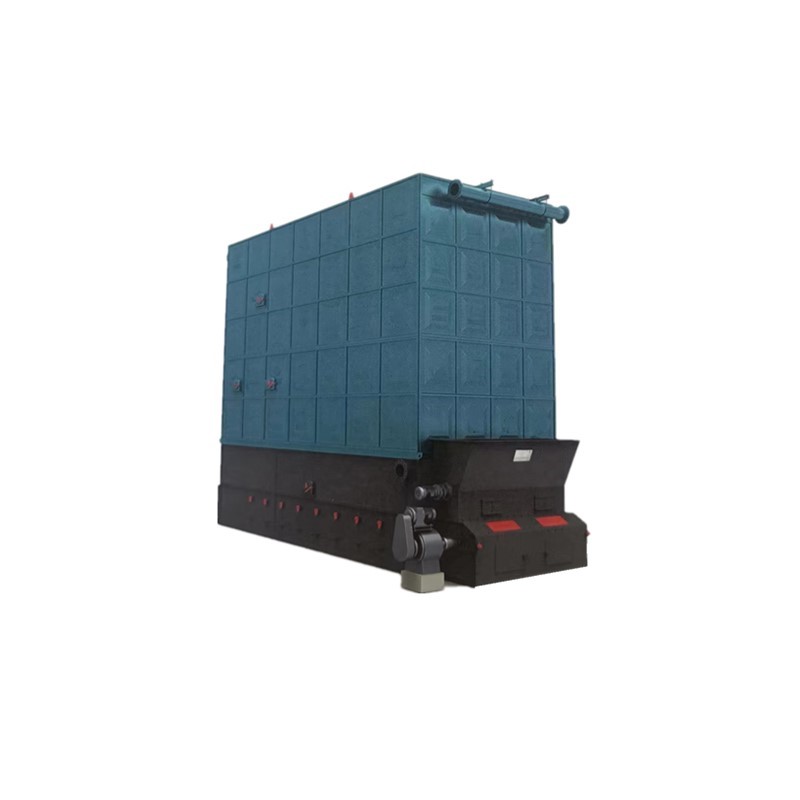
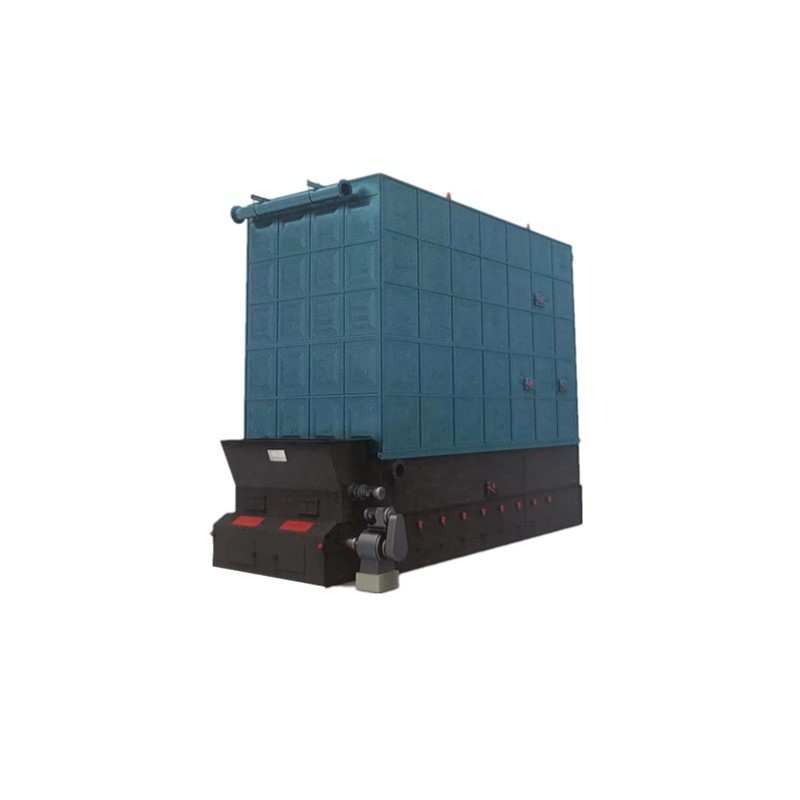
Coal fired Thermic Oil Boiler
Thermal Oil Boiler System
Low pressure high temperature oil for processing
Features
• Application for all industries, such as chemical/petroleum/wood processing industry etc.
• Fuel: firewood, rice husk, palm shell, the other biomass fuels, various coal, such as WII, WIII, AI, coal AII, AIII,H, P
• Rated thermal power: 0.7MW-29.2MW(930HP-38,794HP)
• Rated Work Pressure: 8bar-10bar(116psi-145psi)
• Rated outlet oil temperature: 320℃
• Core Control Mode:PLC control, PLC+PC control, DCS control
• Thermal Efficiency(%):>80%
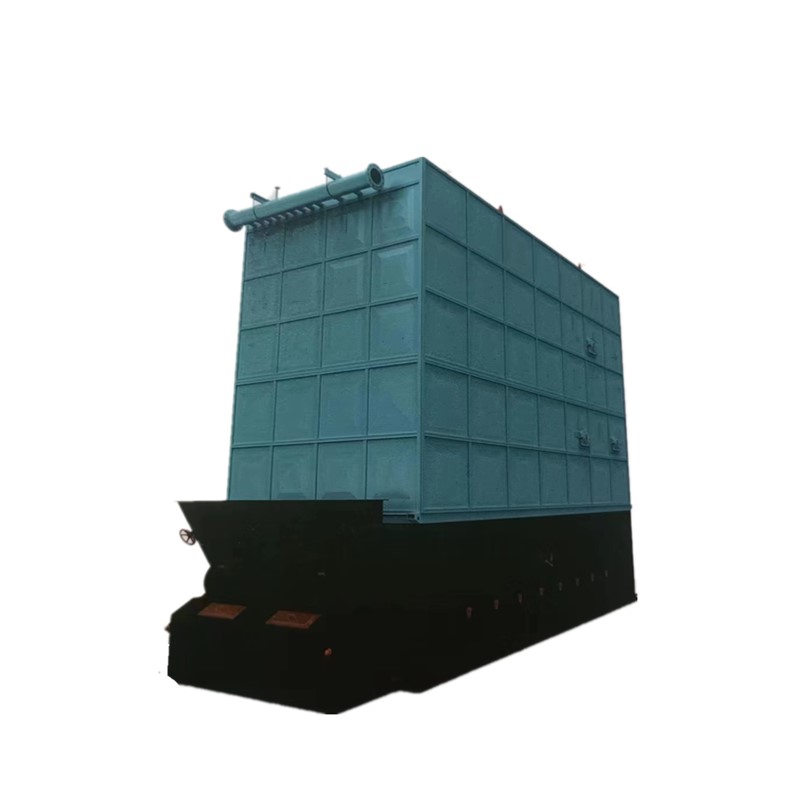
Introduction
Reviews
Thermic Oil Boiler Overview
The YLW series coal/biomass fired thermic oil boiler is a square box type assembled forced circulation chain grate boiler. The thermic oil boiler is made up of the upper body and lower body, lower grate. Thermic oil boiler’s thermal power is below 8200kW, the boiler is whole integrated delivery, above 8200kw, the thermal oil boiler body part and the grate part are delivered separately, then combined at the site. The boiler’s radiant heating surface uses a single furnace or a double furnace in snake-shaped convection heat exchange tube. The tail is equipped with an air pre-heater to reduce the temperature of discharged smoke, improve heat efficiency, reduce fuel consumption, and save energy.
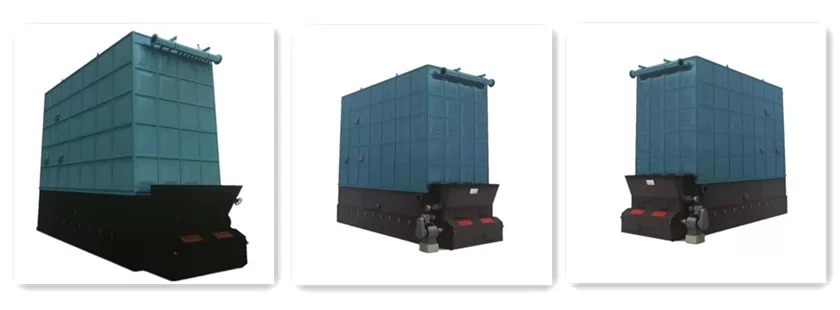
Thermic oil boiler widely is used in the petroleum, chemical industry, chemical fiber, pharmaceutical, textile printing and dyeing, light industry, building materials, wood processing, food, road construction asphalt heating, and other industrial fields that require high temperature heating.
During operation, the fuel drops onto the grate from hopper and fires. The high temperature flue gas is reflected to the front by the rear arch and goes into the furnace, after heat exchange by radiation heating area it goes into the convection heating area, and after heat exchange here, it goes into waste heat boiler, then into air pre-heater, and then goes into dust collector. After the dust collector and drawn by the ID fan, the flue gas is finally emitted into the atmosphere through the chimney.
There are four heating areas in a boiler: furnace radiation heating area, convection tube bank heating area, waste heat boiler, and air pre-heater (economizer).
Thermic Oil Boiler Features
· Combustion room
According to the characteristics of thermic oil boiler and various kinds of fuel, design various kinds of combustion room adapt to ll, IIl bituminous coal, anthracite, and sorts of biomass fuel.
Radiation section:
·Adopt advanced structural style to optimize radiation heating surface and reduce the formation and discharge of flue gas dust in combustion room.
· Convection section
Optimize the convection heating surface and adopt effective fix and structural support to make its working life longer.
· Furnace insulation
Use superior refractory brick to build inside and the concave-convex panel outside and superior perlite in the middle. Keep the thermic oil boiler furnace temperature under 50℃ to make the minimization heat energy loss.
· Partition
Set up effective flue gas partition for convection heating surface and cast partition to make thermic oil boiler work longer and more effectively.
· Ash removing door
Set up an effective ash-removing structure to make it easy to maintain, operate, and clean for a thermic oil boiler.
Thermic Oil Boiler Parameter
Model | YLW-1400 | YLW-2400 | YLWW-2800 | YLW-3500 | YLW-4200 | YLW-6000 | YLW-7000 |
Fuel type | firewood, rice husk, palm shell, the other biomass fuels, various coal, such as WII, WIII, AI, coal AII, AIII,H, P | ||||||
Rated thermal power(MW) | 1.4 | 2.4 | 2.8 | 3.5 | 4.2 | 6 | 7 |
Rated thermal power(^x104kcal/h) | 120 | 200 | 240 | 300 | 360 | 500 | 600 |
Rated outlet oil temperature(℃) | 320 | 320 | 320 | 320 | 320 | 320 | 320 |
Rated working pressure(Bar) | 8 | 8 | 8 | 8 | 8 | 10 | 10 |
Heat efficiency(≥%) | 80 | 80 | 80 | 80 | 80 | 80 | 80 |
System installed capacity(kW) | 55 | 76 | 85 | 105 | 125 | 170 | 193 |
Expansion oil tank(m³) | 2.5 | 2.5 | 3.5 | 3.5 | 5 | 8 | 10 |
Storage oil tank(m³) | 5 | 6 | 8 | 8 | 10 | 15 | 15 |
Max Transportation size:L×W×H(m) | 5x2.25x2.45 | 6.5x2.5x2.8 | 6.5x2.55x3.2 | 7.5x2.55x3.2 | 7.4x2.87x3.3 | 8.32x3.33x3.25 | 9x3.33x3.35 |
Max Transportation Weight( t ) | 11 | 13.5 | 14.5 | 16.5 | 25.5 | 33.5 | 35 |
Note: Parameter is for reference only, if any changes should follow the factory technical data. Thermal efficiency is calculated based on AII |
Composition of Boiler System
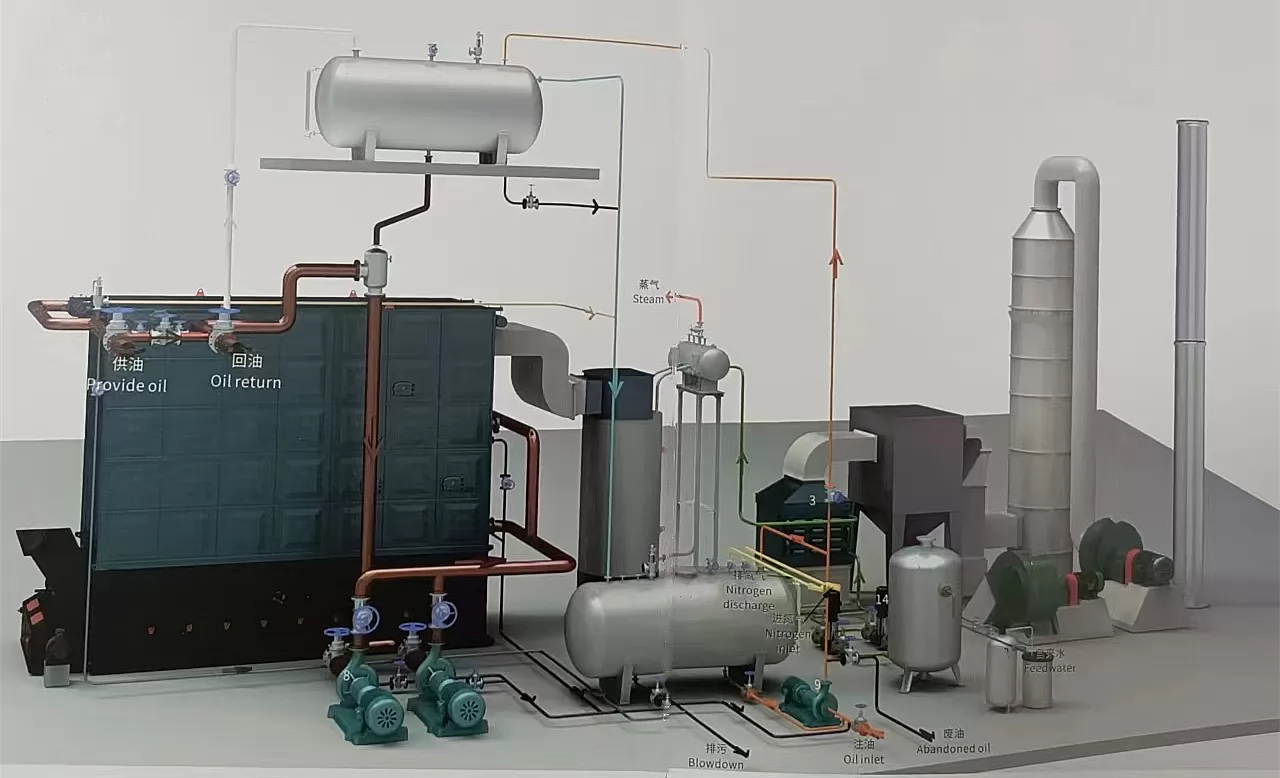
The thermic oil boiler system is compesed of the combustion system, medium oil system, and control system
· Combustion system
The coal/biomass fired thermic oil boiler combustion system is according to the fuel characteristics of the boiler to design furnace arch size, equipped with combustion equipment, Which can realize thermic oil boiler automatic combustion and automatic slag removal function. The combustion system equipment consists of fuel feeder, chain grate, air distribution equipment, coal hopper in front of the furnace, grate speed reducer slag removal equipment, etc.
· Medium oil system
The medium oil system consists of injecting the oil part and circulating the oil part.
The injecting oil part: injecting oil refers to medium oil that is provided to the boiler for hot oil conversion. The injecting oil channels oil into the boiler and automatically controls it to satisfy make-up oil requirements for the system. Such as due to the high temperature oil expansion in the system, or boiler blow-down, the whole system needs fresh thermal oil to inject.
The circulating oil part: the circulating oil is part of the boiler responsible for collecting and regulating the high temperature oil generated by the boiler. Valves and pressure gauge controls are used to monitor and regulate temperature and pressure.
The medium oil system equipment consists of a boiler body, expansion tank, oil storage tank, circulating oil pump, injecting oil pump, oil gas separator, and other equipment, and oil pipelines. The heat medium oil is injected into the boiler by the circulating oil pump, and after being heated, it is transported to the heat-using equipment through the oil supply pipeline, and the heat medium oil after heat release returns to the circulating oil pump through the oil return pipeline to enter the re-circulation.
· Control system
The thermic oil boiler control system is a collection of boiler electrical control components, a center for collecting and processing boiler operating signals, and an operation platform for sending execution instructions to each execution unit of the boiler.
CN Boiler has always adhered to the concept of electrical full integration in the industrial energy industry, that is, integrating strong and weak current systems such as boiler control, boiler room auxiliary machine control, upper monitoring system, and boiler room power distribution system into a complete electrical package, forming a characteristic industrial energy control system (CN Boiler Multi-Boiler Control System, referred to as CN Boiler- MBCS). The control system is shown as follow:
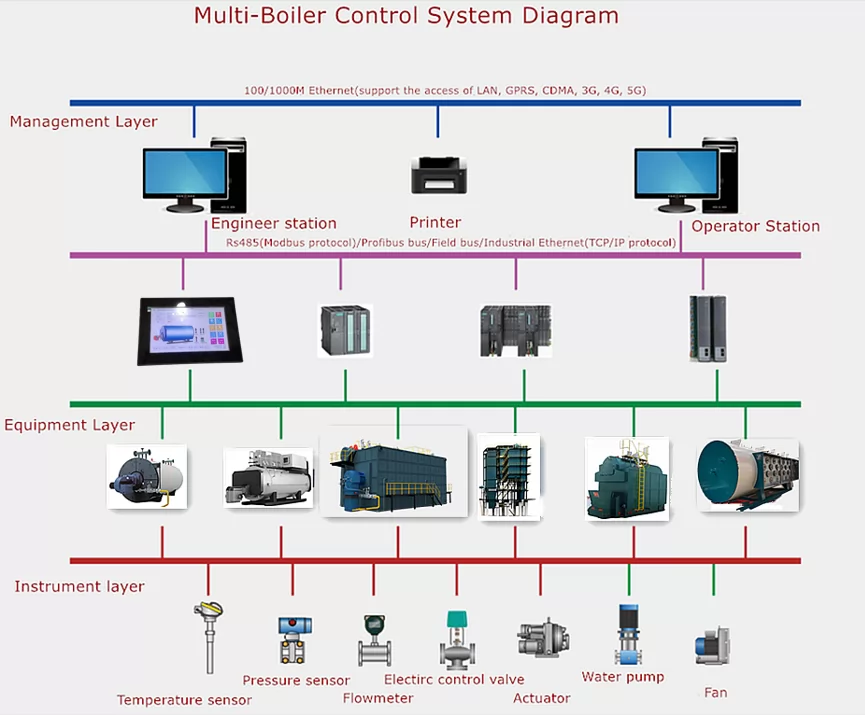
The control system of coal/biomass fired thermic oil boilers provides the control of boiler temperature, pressure, burning, safety protection, and so on.
The thermial oil boiler system control principle: Through the real-time data collection, monitoring, and processing of boiler water level, pressure, flue temperature, and burner, the purpose of intelligent and safe operation is achieved.
★ The Core Control Mode of the hot oil boiler system: Integrated controller (All-in-one PLC, not programmable), PLC control(programmable), PLC+PC control, DCS control.
★ Standard Control Content: boiler level, pressure control, alarm, and interlock, and set up an automatic control system for combustion start and stop.
★ Boiler Control Modes of Operation: Automatic and Manual
a) The boiler in automatic mode is in a fully automatic operation state,
b) Manual mode: The operation of the boiler equipment is controlled by manual operation. Under normal circumstances, the boiler should operate in an automatic operation state. In special cases, it will be required to switch to the manual state.
★ Control system detection data sources: burners, temperature sensors, pressure transmitters, pressure controllers, liquid level gauges, hot oil flow meters, electric control valves, and other remote instrument valves.
Types of control cabinets for thermic oil boilers: wall-mounted control cabinet, podium control cabinet, MCC vertical control cabinet, piano-style control cabinet, positive pressure explosion-proof control cabinets, and three-proof control cabinet.
Each control cabinet we leave the factory has a unique number, and it has the function of mobile phone viewing. You can see the operating status of the boiler in real-time, such as temperature, water level, pressure, alarm record, etc. But the actual operation still needs to be completed by the staff in the boiler room.
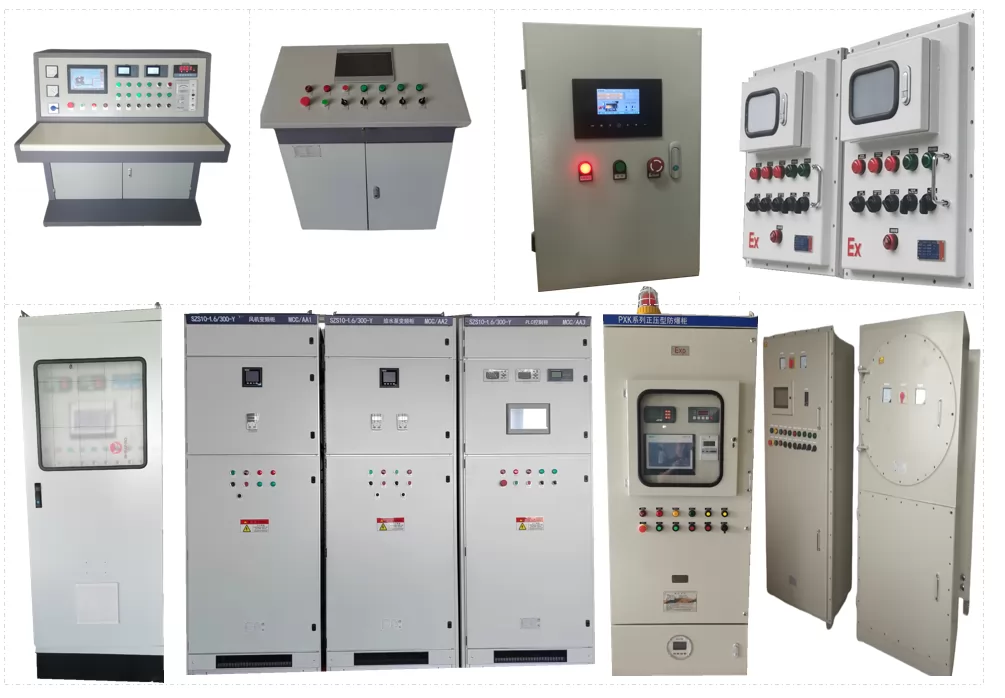
Company profile
CN BOILER ENGINEERING SOLUTION LLC is a comprehensive service provider of thermal energy systems in China, devoted to providing customers with one-step thermal energy system solutions by safe, save energy, environmentally, intelligent, and reliable. Main products include industrial boilers(hot water boilers, steam boilers, thermal oil boilers, waste heat boilers, and CFB boilers), steam generators(electric steam generators, electric hot water generators), intelligent control system by PLC control, PLC+PC control or DCS control, remote instrument and valves, and so on. The control system includes industrial boiler control system(oil fired boilers, gas fired boilers, biomass fired boilers, coal fired boilers, electric boilers, waster heat boilers, CFB boilers), PLC deaerator control system, condensate recovery system, reactor control system, heating exchanger control system, hot air boiler control system etc. The remote instrument and valves include temperature sensors, pressure transmitters, pressure sensors, pressure controllers, liquid level meters, flowmeter, electric control valve, Zirconia, TDS sewage, and so on.
Share your thoughts
Showing
6
of
0
reviews
Most recent
Top Reviews
Read more
Your rating
Your review *
Name *
Enter your Name
Email *
Enter your Email
Upload Image
Notice: Ensure your image is no larger than 200KB before uploading.
Submit
Contact Us Now
Enter your inquiry details, We will reply you in 24 hours.
Name can't be empty
E-mail can't be empty
Company can't be empty
Phone can't be empty
Phone
Products can't be empty
Products you want
Message can't be empty
Verification code error
Clear
People who viewed this item also viewed